New NPI award-winning 3Di Series – a future-proof evolutionary inspection system
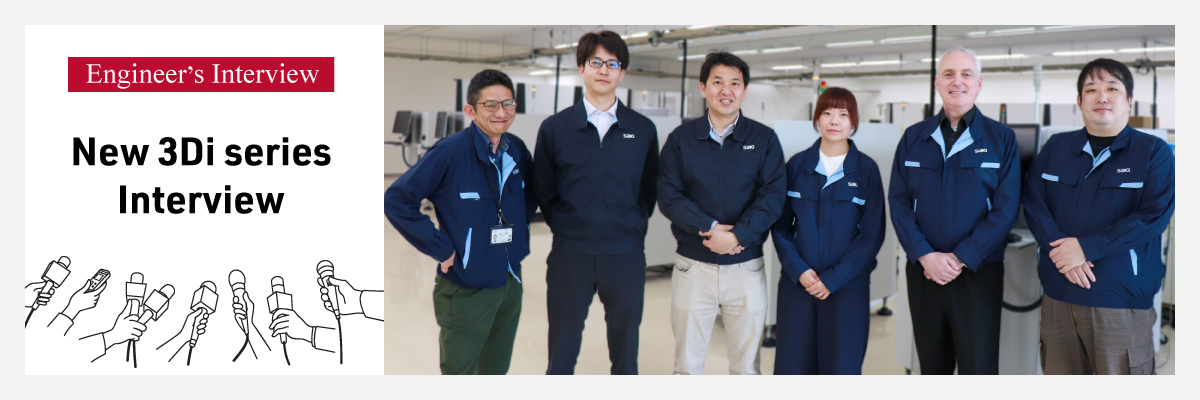
The rapid progress of surface mount technology in recent years has expanded the market for high-speed and high-resolution inspection. Meeting these demands is Saki’s new 3Di Series.
For its combination of high-speed and high-resolution inline 3D-AOI, Circuits Assembly Magazine honored Saki with the New Production Introduction (NPI) Award 2023 for “Inspection Equipment – AOI Systems”.
We interviewed our developers to find out more details about what goes on behind-the-scenes:

Congratulations on winning the NPI Award 2023!
Could you tell us how the development of the New 3Di series came about?
Y Thank you.
The starting point for the New 3Di Series was when I felt that the speed of technological innovation in the industry kept increasing.
When looking at trends in the semiconductor industry, it is not difficult to predict what is coming in the next couple of years; however, looking to predict new technologies and products that may come in the next five to ten years is a lot more difficult, simply due to this rapid acceleration of technological innovation. With this in mind, it would be extremely challenging for us to keep up with market trends with our previous 3D-AOI model.
We needed a new model that would be as significant ten years from now as it is today, with continous upgradability to maintain its premier performance. This is what we now have with the New 3Di Series.
When you started the New 3Di Series project, what did you think would be the increasing needs for the future?
Y There will be an increasing demand for component miniaturization, which leads to our belief that there is a need for single-digit resolution, essential for inspecting 0201mm components. However, this focus on high-resolution was not our only consideration and we recognized that high-speed is still a very important factor for our customers.
Thanks to our line scan technology, Saki products are recognized in the marketplace as being extremely fast – we have no desire to lose that position to our competitors.
Throughout our global market research, we determined that both “high-resolution” and “high-speed” were essential factors for our new inspection system. From this research and a greater understanding of market trends, we decided to develop two models:
The first is a machine focused on high-resolution, designed to achieve superior performance for high-density assembly of miniaturized components; the second a high-speed model that can handle components down to 0402mm, with a focus on speed-orientated mass production.
So, in summary, the concept of the New 3Di Series is a combination of both “high-resolution” and “high-speed”?
Y While those two characteristics are significant aspects, the concept for the series is something else.
As I mentioned earlier, it is important to maintain performance for an extended lifespan of the machine – it is essential that these machines are still market leaders in ten years or more.
The new 3Di Series machines are designed with our “upgrade concept” in mind to provide additional value for our customers, who will be able to apply options and future upgrades to the existing technology. We hope that through these upgrades, our customers will continue to enjoy peak performance even after ten years of continued use.
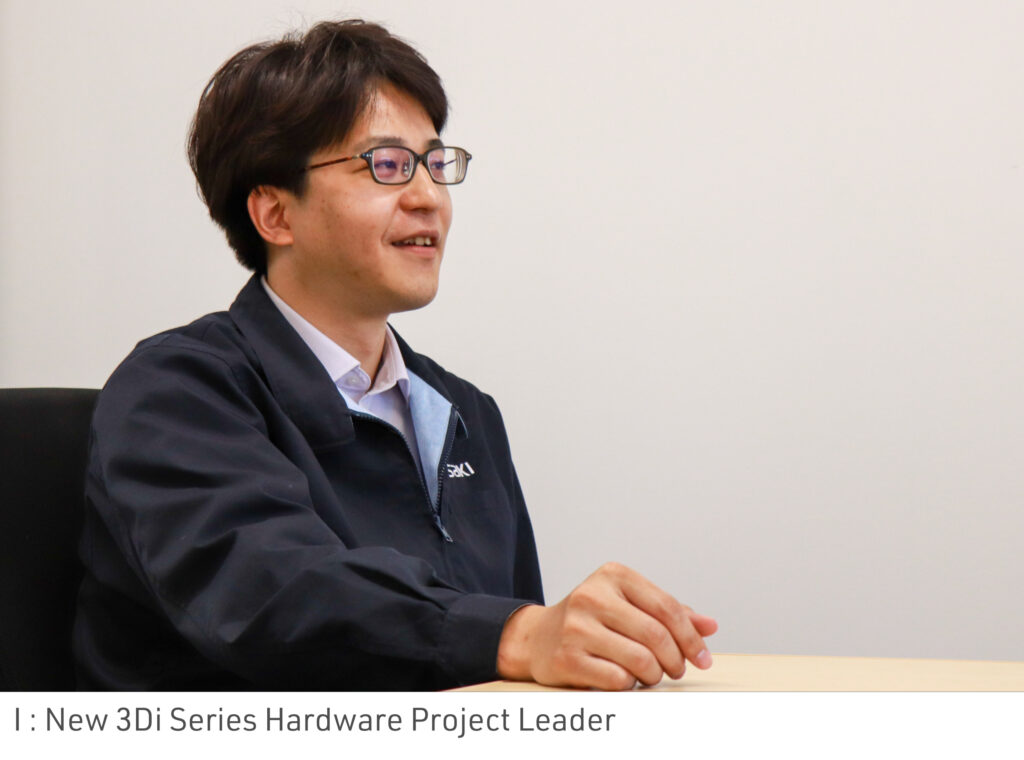
Could you tell us more about the “upgrade concept”?
Y One specific example is how we enable the customers to directly upgrade the cameras of the new 3Di system. We had a primary focus to enhance the camera as it has a significant impact on the final inspection performance. Generally, the release cycle for new camera models is between three to five years so, considering the operational lifespan of the machine, we designed the hardware with a rigid long-lasting frame to allow for two to three camera upgrades. The high rigidity frame is able to endure for over 15 years and ensures stability in the machine performance – it is this that allows multiple camera upgrades to the latest model without ever compromising functionality.
I The optical design has been structured to allow for easy on-site upgrades. This is not only for the camera but for upgrades of other optical components that will be released in the future.
Hearing your description, it sounds like there is a demand for camera replacement.
K Yes. While it is a slightly separate topic from upgrades, there already seems to be demand for camera resolution switching in the market. Customer feedback has previously featured comments such as “it would be nice to change the resolution depending on the product”. On-site camera switching is an additional feature incorporated into the New 3Di Series that has been developed thanks to this important feedback.
Y The idea of the “upgrade concept” is meaningless if replacing the camera is too difficult. Both the existing cameras and those coming in the future should be easily replaceable on-site, allowing for immediate operation. We believe that an easy exchange process that can be done by the customer is important – without this, it is simply unproductive.
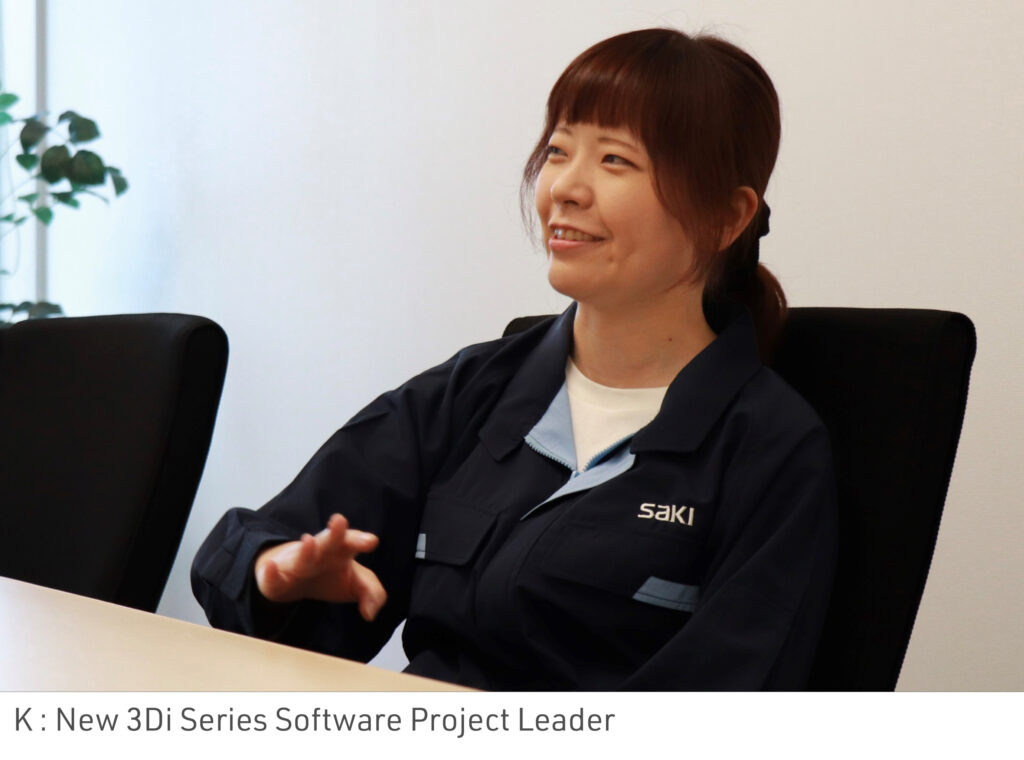
I The current model allows for the camera to be switched in just 30 minutes, with the additional calibration bringing the total time to around 90 minutes for the entire process. If all goes smoothly, it can often be less than this. For many, this means all the necessary steps can be completed during a slightly-extended lunch break!
Are there any other benefits of the “upgrade concept”?
K Absolutely. One advantage that customers will discover is when they are creating inspection data.
When transfering to new equipment, creating a new inspection program, or converting and moving that asset, is a challenging task. With the New 3Di Series and the upgrade concept, we can consistently deliver the latest inspection capabilities without changing the machine or the inspection program. This offers significant advantages for both our current customers already using Saki equipment and potential customers considering our machines for the future.
Y The upgrade concept will result in an immediate cost reduction. In the past, when there was a change in the inspection objects, it required purchasing two machines. With the New 3Di Series, customers only need a single machine with two different resolution heads; a significant saving in investment. This approach also allows for saving when considering machine disposal at the end of the lifecycle.
That’s true. However, it seems that Saki doesn’t have any advantage in terms of cost.
Y If the unit price of the product is the only consideration, of course sales will drop. However, we will gain increased orders from customers who resonate with the upgrade concept. Through this, we can leverage economies of scale to increase profit margins.
Another competitive advantage for us is that manufacturing costs and space requirements are also both reduced as the machine assembly footprint is lowered, as well as the time and workload required to complete each machine.
I see. It is a great plan that will bring benefits to both Saki and its customers.
Did you face any challenges during the development process?
I Balancing to achieve better resolution, faster cycle time, and a deeper depth of field was a challenging task for us. In principle, there is a trade-off between higher resolutions and cycle time; it was a significant challenge for us to enhance all of these aspects together to improve on the previous model.
How did you overcome the problem?
I It is all about optimization. We designed the machine to harmonize and enhance the effect of the essential components responsible for defining the overall performance of the camera, lens, and other optical elements, while ensuring there is no degredation elsewhere.
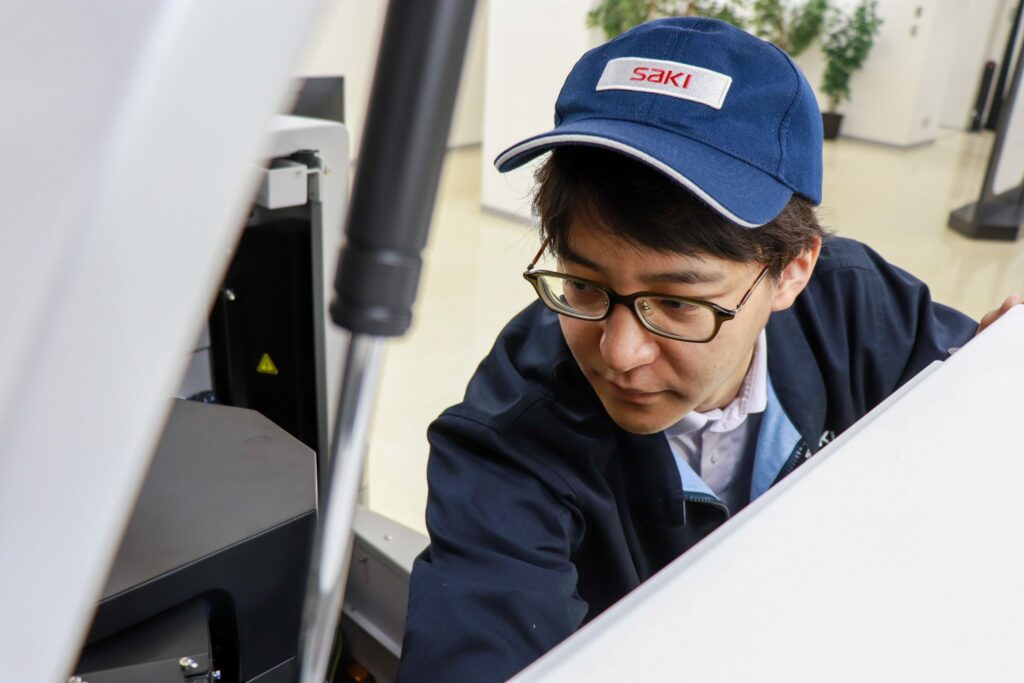
Were there any challenges from a software development perspective?
K Yes, there were definitely challenges on the software side!
As the performance of the optical system improves, the software needs to improve its inspection capabilities accordingly. The accuracy of the measurement matters in inspections and, when extending the maximum height measurement range up to 25mm (a 5mm improvement on the previous model), achieving absolute accuracy was difficult due to image stability in the extended height area.
Improving cycle time was another challenge; with higher resolution came a great deal more data that needs to be processed.
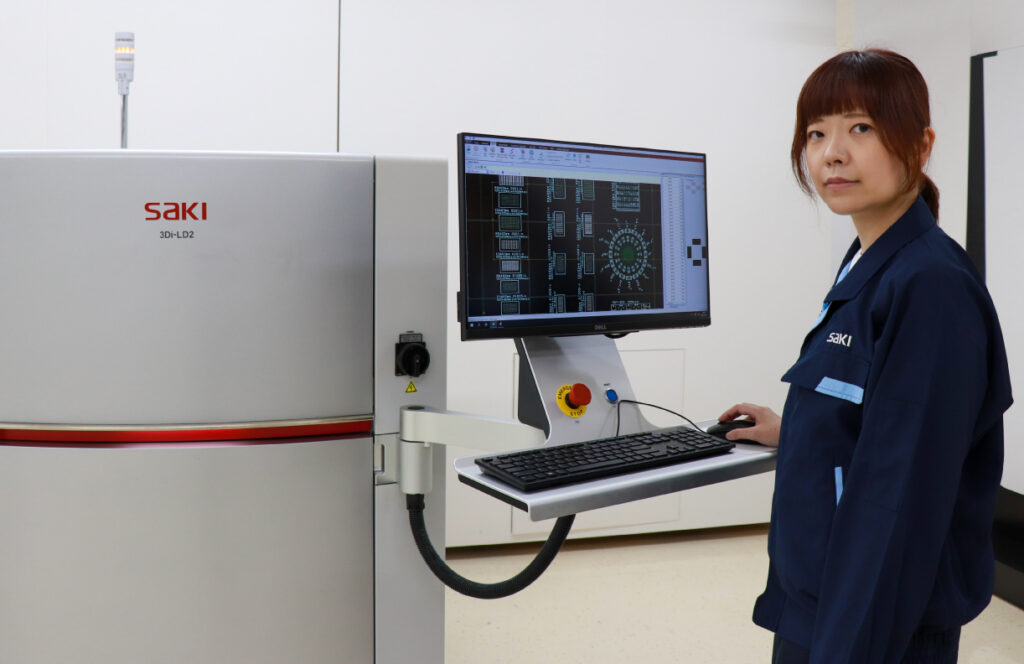
How were these overcome?
K One significant development was a new noise reduction method in the 3D image reconstruction process. This improvement resulted in a significant reduction in noise, which allowed us to achieve the accuracy we needed when expanding the measurement range to 25mm.
For the data processing, we worked on improving both the hardware and the inspection algorithm, which worked to reduce the cycle time.
A key advantage with Saki products is that all the related processes, such as height map generation, image processing, and the consistent image capturing process, are all developed by ourselves in-house. This means it is easier to improve and upgrade performance.
It is thanks to these improvements that we reached 4,500 mm2/sec in high-resolution 8um, and 7,000 mm2/sec with the 15um camera.
Is there a market demand for the height measurement range extension?
K Absolutely. The number of cases where smaller and taller packages are being mounted in the same area is increasing. These require the extension of the height measurement range in high resolution. Saki recommends customers use a combination of the 8um camera with the Z-axis option to fulfil both requirements of high-resolution and extended height measurement.
The height measurement range is extended to 25mm with the 8um resolution camera, and it is further increased to 40mm when combined with the Z-axis option. Thanks to this, the inspection of solder for small packages and tall components can be performed at the same time. By extending the height measurement range, the inspection scalability is also extended for THT components, press-fit components, and dynamic automatic PCB surface height correction.
The New 3Di Series can flexibly respond to customer demands and provide optimal solutions by combining these optional fuctions, such as Z-axis with upgradable parts.
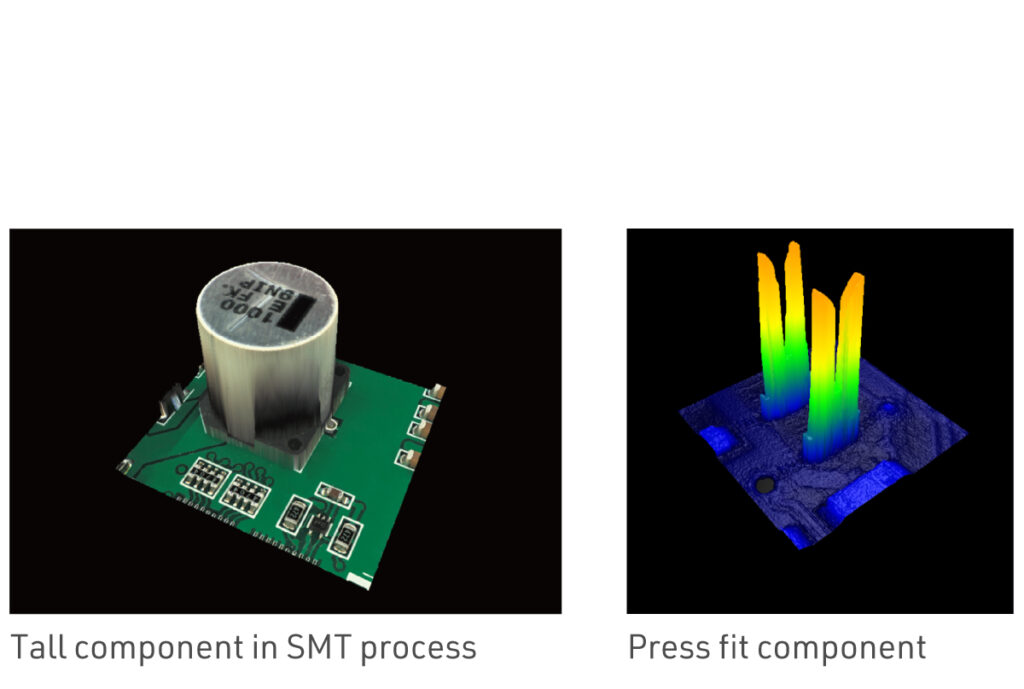
Shifting the topic, let me ask your mindset as a developer. The New 3Di Series is a highly unique product – where does your inspiration come from for its development?
Y Above all, it comes from the customers. It is really important to talk to both the customer support team and the sales team to get a true understanding of the customer’s requirements. I have daily briefing meetings with them and often hear “Can we provide a solution for this request?” or “I’m facing some difficulties with this”. In the later stages, when considering various aspects of the development, I often came up with ideas that were to find specific solutions for specific requests, or further improvements to address their difficulties. Eventually, these ideas would be implemented into the new system.
I continue to actively engage in this level of communication with our teams and the customers to ensure future synergy.
K I also agree with Y. For the New 3Di Series, we incorporated a lot of feedback from the technical sales team into the product development. Comments such as “it was difficult to inspect this customer’s board” or understanding the latest trends as described by our demo specialist helped provide perspective.
The same is true on a larger, global scale. We encourage feedback from our customers everywhere. We know that not everything does get reported back, so one current challenge is uncovering exactly what customers really struggle with.
I I have a slightly different mindset from both of you. I prioritize optimization by considering the conditions and limitations we have. It is my goal to maximize performance using the available resources and I believe it is important to focus on the creation of “new value” at each next step. I’m satisfied with the optimization of our new product that leads to faster cycle time, higher resolution, a deeper depth of field, and the extension of the height measurement range. Of course, I understand the importance of meeting the needs of our customers, but it is also important to proceed with the project in a well-balanced way that considers our own situation.
In conclusion, if you have any further prospects to share, please tell us.
Y I’d simply like to develop something that the customers really need.
K From a software development perspective, there are several initiatives that we would like to pursue for quality improvement. It is our goal to reorganize our internal structures to speed up development in the future.
I I have a lot of things on my mind: designing parts that are easily and quickly replaceable, modularization, and many more improvements. I’m also interested in contributing to the improvement of inspection capability from the hardware development side.
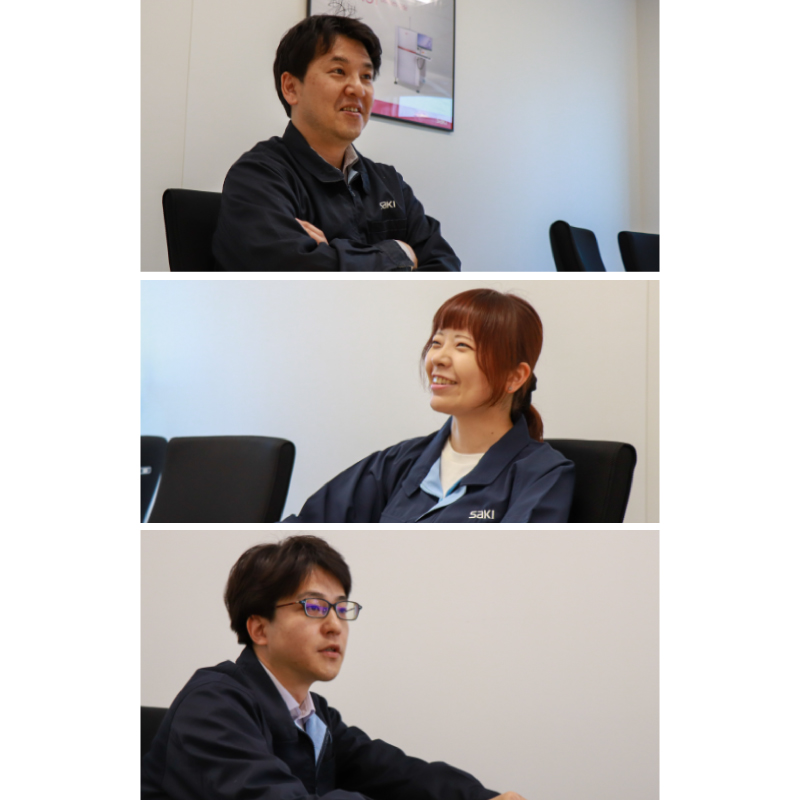
It was a great opportunity for me to hear these inspiring stories about the New 3Di Series – and to understand why it achieved the NPI Award 2023. The latest inspection systems are expected to have speed and accuracy as standard, along with flexibility and grown capabilities to keep up with technological advancements. In response to this technology evolution, Saki has embraced the “upgrade concept”, inspired by the feedback and needs expressed by customers and the market. Saki continues to tackle challenges together with our customers, all leading to the creation of new value.
Thank you all very much.
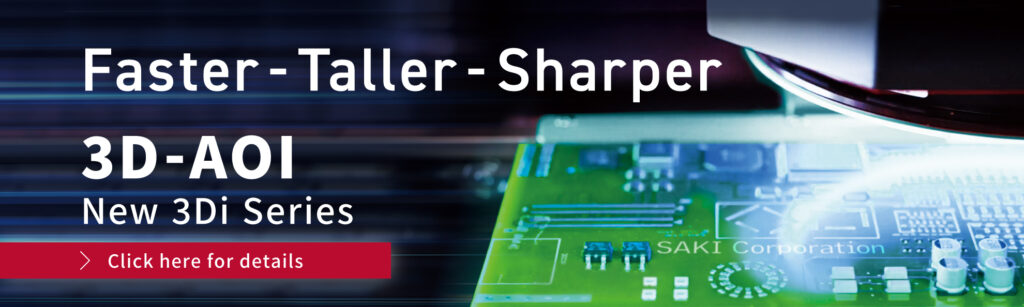