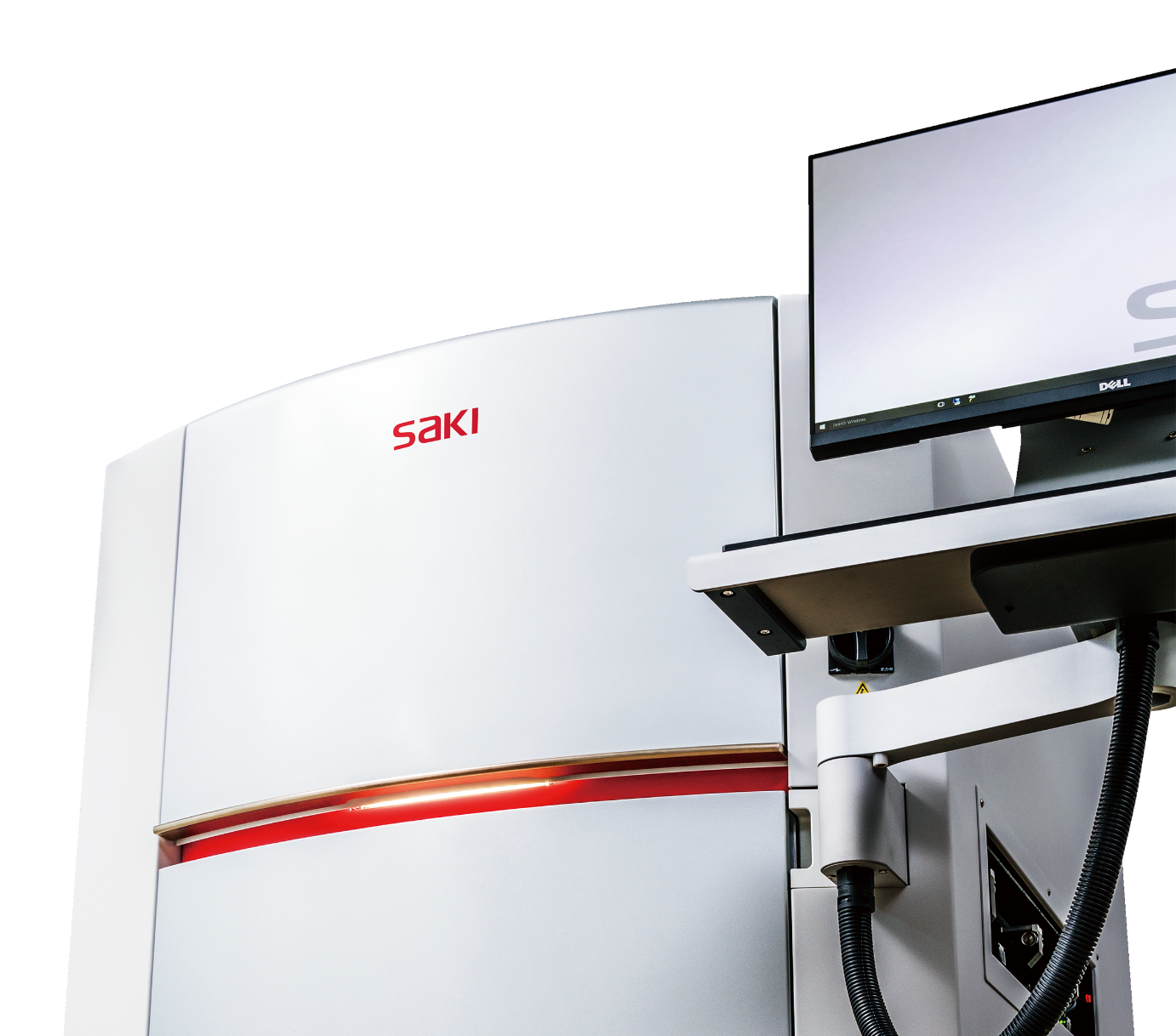
3D Solder Paste Inspection
Machine
3D-SPI
Saki’s high-speed, high-precision 3D-SPI machines specialize in the inspection of SMT process solder printing. 3D-SPI machines inspect and analyze a wide range of potential problem points, including the measurement of solder paste area, height, and volume; as well as bridge, solder horn, and BGA coplanarity compliance.
The quality of the entire production line is ensured through machine-2-machine co-ordination with solder printing and pick-and-place machines.
Hardware designed for high-speed and high-accuracy inspection
The design employs an ultra-rigid gantry and biaxial drive with an ultra-high-definition linear scale, enabling high-speed movement of the optical head with incredible stopping position accuracy.
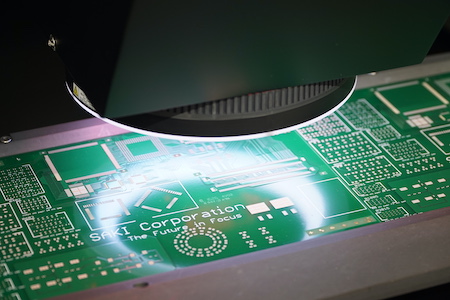
Faster data processing thanks to Saki’s unique dedicated software
All imaging and processing software is developed by Saki in-house, improving hardware optimization and inspection algorithms – leading to faster, superior data processing.
Robust hardware structure that guarantees an extended lifetime of continued high-quality inspection
With its ultra-rigid gantry, biaxial drive, and ultra-high-definition linear scale, the 3D-SPI has high repeatability and contributes to maintaining the stability and quality of inspection result data. Stable inspection is guaranteed thanks to the strong, durable frame that provides reliability for 15 years and beyond.
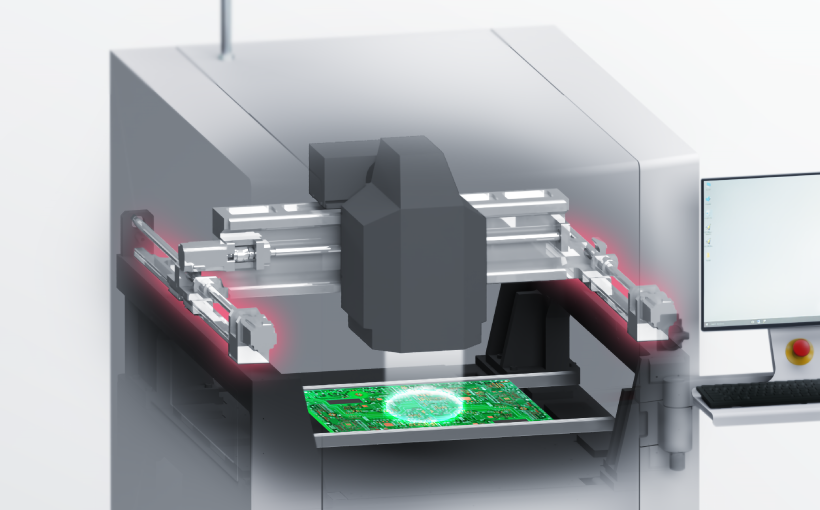
Self-diagnostic system
The self-diagnostics monitor equipment status in real time. Hardware checks during startup and prior to inspection greatly reduce the risk of sudden failures, and combined with consumable monitoring, allows maintenance to be efficiently scheduled with minimal downtime.
Time-Based Maintenance
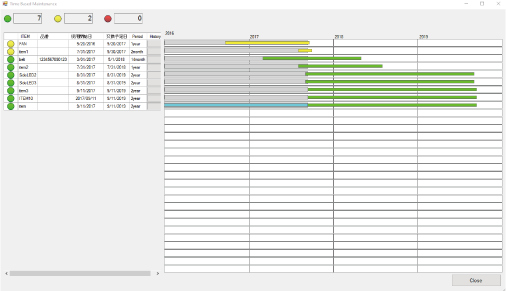
Condition-Based Maintenance
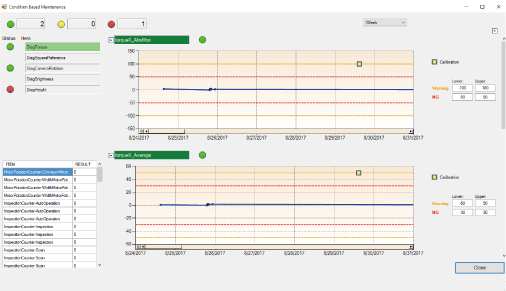
Solder print inspection algorithms
IPC-compliant inspection quality
Positional deviation of pad size is inspected based on the IPC-7527 quality standard for measurement allowances.
IPC-7527 Quality Standard Inspection
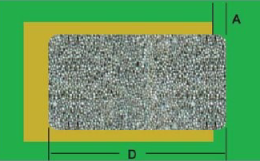
Printing Deviation Standard
Paste solder protruding from the pad Class 1,2,3: less than 25%

Actual Image
Coplanarity inspection
High I/O count device inspections benefit from improved coplanarity, with solder range analysis for height, volume and area that helps prevent post-reflow wetting.
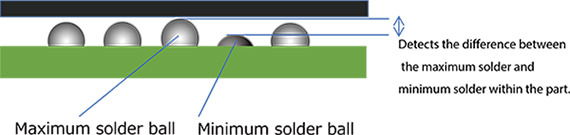
SPC functions for visualization of solder quality
Solder quality is managed and maintained through comprehensive monitoring of board solder amounts and defect trend analysis. Extensive reporting functions and data analysis tools allow for export of defect type rankings and yield charts.
Defect Analysis
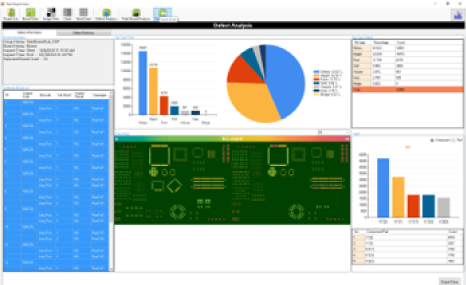
Yield Chart
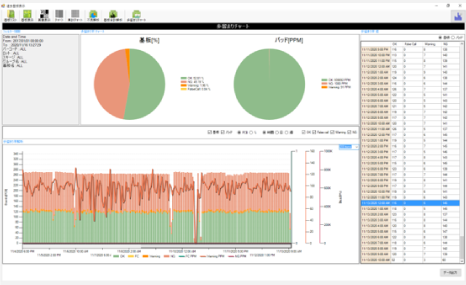
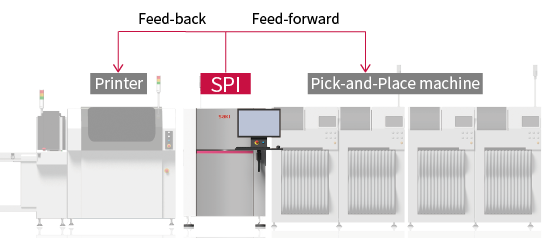
Feed-back from SPI to screen printer
The accuracy of solder printing is improved thanks to feeding back solder printing position misalignment data from the SPI to the solder printing machine. Additionally, metal mask cleaning instructions are automatically communicated to prevent solder printing defects.
Correction of the Print Position
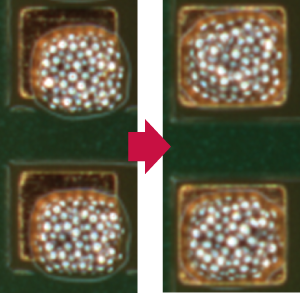
Automatic Cleaning Instructions
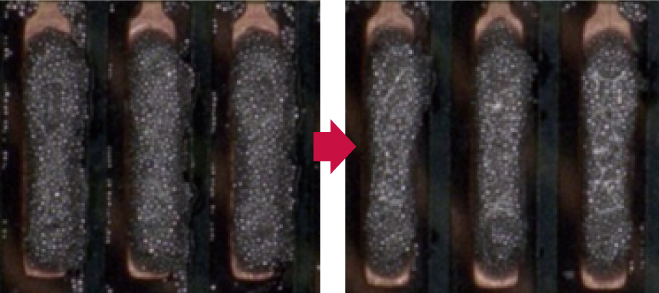
Feed-forward from SPI to pick-and-place machine
Component mounting position is corrected by sharing information on solder printing position misalignment with the pick-and-place machine. Additional data on failed sub-boards is also communicated to avoid mounting components in these instances.
NG Board Skip
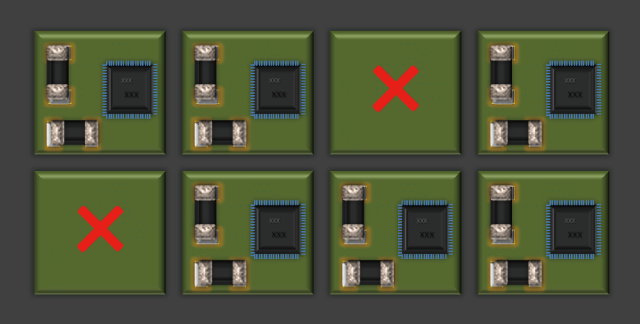
Saki’s Total Lineup Solution
Saki’s 3D-AOI uses a common platform with 3D-SPI and 3D-CT-AXI. The process is consistent throughout – from post-printing solder inspection using SPI, through to the inspection of mounted components.
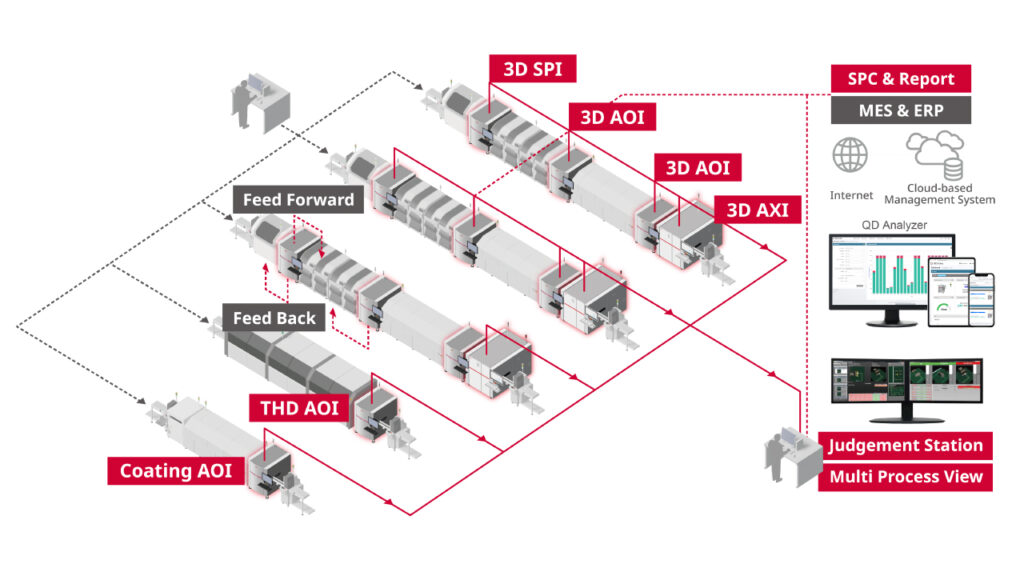
Specifications
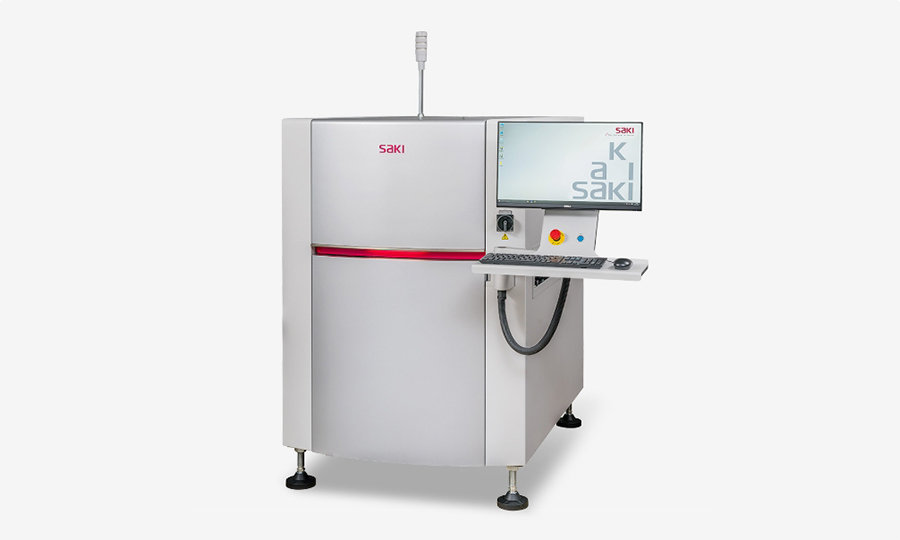
3Si-LS3EX (L size・Arm type)
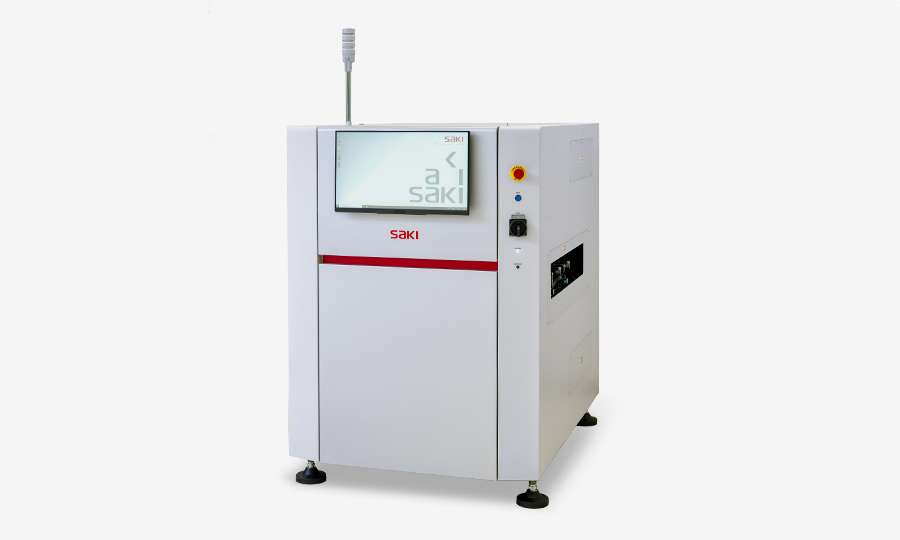
3Si-LS3EX (L size・Built-in type)
Specification
Dimensions | M | L | XL |
---|---|---|---|
Model | 3Si-MS3EX | 3Si-LS3EX | 3Si-ZS3EX |
Size[Main body] (W) x (D) x (H) mm (in.) | 850×1480×1500 (33.46 x 58.27 x 59.06) | 1040×1480×1500 (40.94 x 58.27 x 59.06) | 1840×1480×1520 (72.44 x 58.27 x 59.84) |
Resolution | 8μm、15μm | 8μm、15μm | 15μm*1 |
PCB Clearance mm (in.) | Top: 40 (1.57) Bottom: 60 (2.36) *2 | ||
Electric Power Requirement | Single-phase ~ 200-240V+/-10%, 50/60Hz | ||
PCB Size (W)×(L)mm (in.) | 50 x 60 – 330 x 330 (1.97 x 2.36 – 12.99 x 12.99 ) | 50 x 60 – 510 x 510 (1.97 x 2.36 – 20.07 x 20.07)*3 | 50 x 60 – 686 x 1016 (1.97 x 2.36 – 27.00 x 40.00)*4 |
Weight | 850kg | 900kg | 980kg |
Inspection Item | the measurement of solder paste area, height, volume, bridge, solder horn, BGA coplanarity compliance |
Dimensions | M |
---|---|
Model | 3Si-MS3EX |
Size (W)×(D)×(H)mm (in.) (in.) | 850×1480×1500 (33.46 x 58.27 x 59.06) |
Resolution | 8μm、15μm |
PCB Clearance | Top: 40mm(1.57 in.) Bottom: 60mm(2.36 in.) *2 |
Electric Power Requirement | Single-phase ~ 200-240V +/-10%, 50/60Hz |
PCB Size (W)×(L)mm | 50 x 60 – 330 x 330 (1.97 x 2.36 – 12.99 x 12.99) |
Weight | 850kg |
Inspection Item | the measurement of solder paste area, height, volume, bridge, solder horn, BGA coplanarity compliance |
Dimensions | L |
---|---|
Model | 3Si-LS3EX |
Size (W)×(D)×(H)mm (in.) (in.) | 1040×1480×1500 (40.94 x 58.27 x 59.06) |
Resolution | 8μm、15μm |
PCB Clearance | Top: 40mm(1.57 in.) Bottom: 60mm(2.36 in.) *2 |
Electric Power Requirement | Single-phase ~ 200-240V +/-10%, 50/60Hz |
PCB Size (W)×(L)mm | 50 x 60 – 510 x 510 (1.97 x 2.36 – 20.07 x 20.07)*3 |
Weight | 900kg |
Inspection Item | the measurement of solder paste area, height, volume, bridge, solder horn, BGA coplanarity compliance |
Dimensions | XL |
---|---|
Model | 3Si-ZS3EX |
Size (W)×(D)×(H)mm (in.) (in.) | 1840×1480×1520 (72.44 x 58.27 x 59.84) |
Resolution | 15μm*1 |
PCB Clearance | Top: 40mm(1.57 in.) Bottom: 60mm(2.36 in.) *2 |
Electric Power Requirement | Single-phase ~ 200-240V +/-10%, 50/60Hz |
PCB Size (W)×(L)mm | 50 x 60 – 686 x 1016 (1.97 x 2.36 – 27.00 x 40.00)*4 |
Weight | 980kg |
Inspection Item | the measurement of solder paste area, height, volume, bridge, solder horn, BGA coplanarity compliance |
*1 Imaging speed when equipped with a Z axis. The XL size comes standard with a Z axis.
*2 For dual mode, the PCB Clearance Bottom is 50mm (1.96 in.).
*3 For dual mode, the PCB Size is 50×60〜320×510 (1.97 x 2.36 – 12.60 x 20.07)
*4 An expansion to 60 inches (686 x 1524) is optional.
Use Case
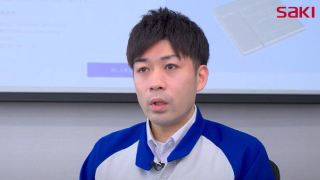
Alps Alpine Co., Ltd.
Alps Alpine Co., Ltd., a global company operating a business centered on electronic components and automotive information systems, has installed Saki’s SPI and AOI.
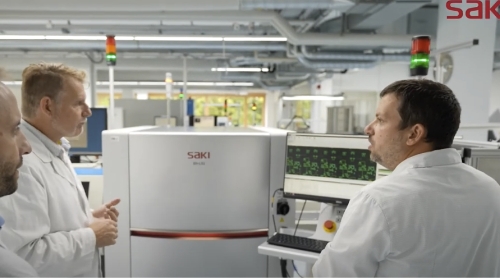
TQ-Group
TQ-Group, a major German electronics solution provider, has installed Saki’s 3D-AOI and 3D-SPI.
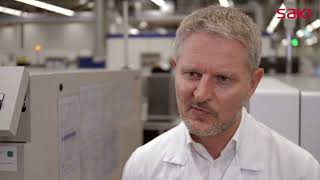
Rohde & Schwarz
Rohde & Schwarz, a major German electronics solution provider, has installed Saki’s 3D-AOI and 3D-SPI.
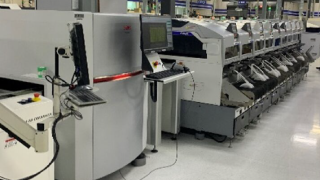
Smart Modular Technologies
Smart Modular Technologies, manufacturer of high-performance DRAM modules and solid-state disk drives (SSDs), has installed Saki’s 3D-AOI and 3D-SPI.
Related Solutions
3D-AOI
3D Automated Optical Inspection Systems
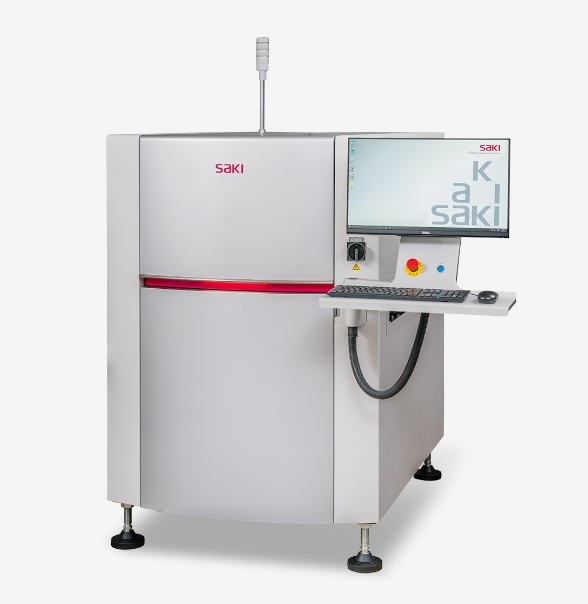
3D-CT AXI
Inline 3D-CT Automated
X-ray Inspection Systems
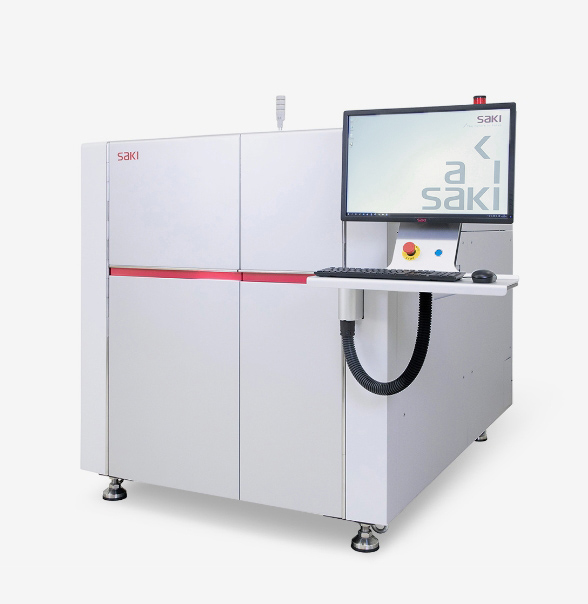