Quality Driven Production
Announcement
2D-AOI Products Discontinuation Announcement
>View more
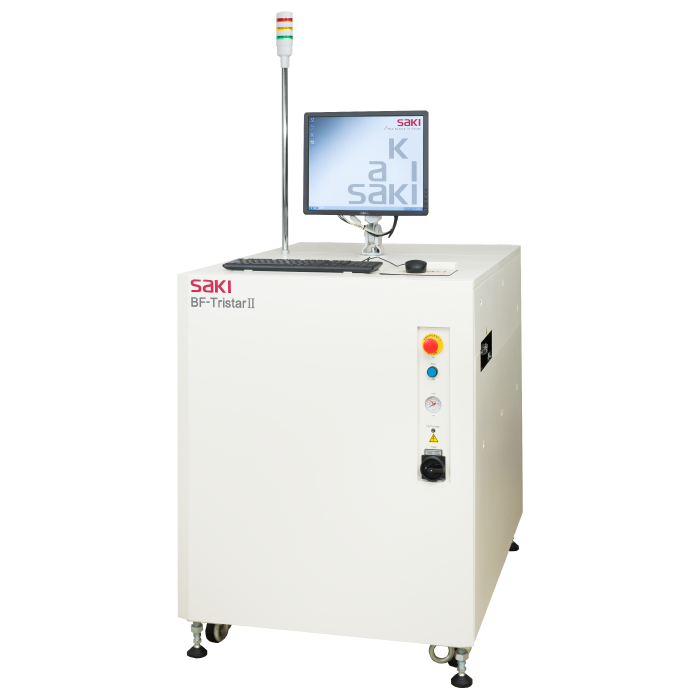
New SPI / AOI release
Saki’s SPI/AOI provides new value with Upgradeable Hardware Design
>View more
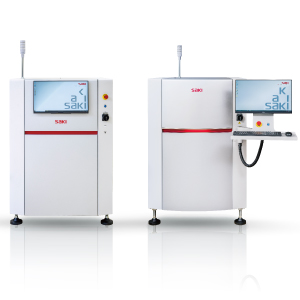
Use Case
Alps Alpine has installed Saki’s 3D-SPI, 3D-AOI, AI Solution
>View more
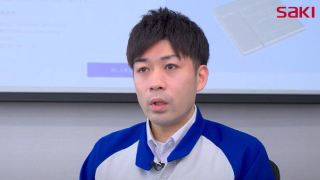

Superior Product Quality
High-accuracy, high-speed and easy to use Saki provides complete inspection solution for any application.
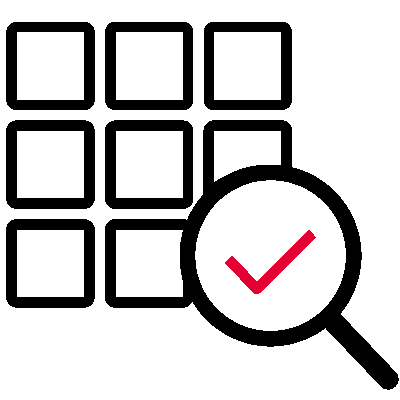
Total Inspection Line Solution
A wide variety of inspections are possible through the development of SPI, AOI, and AXI.
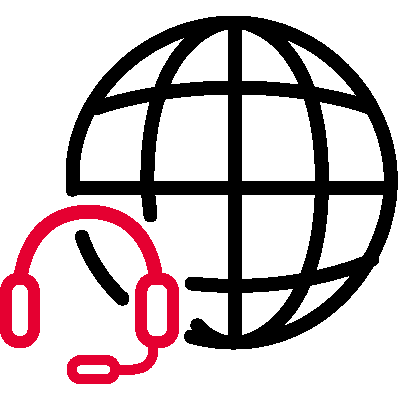
Technical Support Satisfaction Guarantee
Global Customer Support Services network guarantees prompt and efficient response in every time-zone.
Technology
High-speed inspection technology
Saki has attained significant improvements in speed while maintaining inspection accuracy by developing all key technologies of products in house.
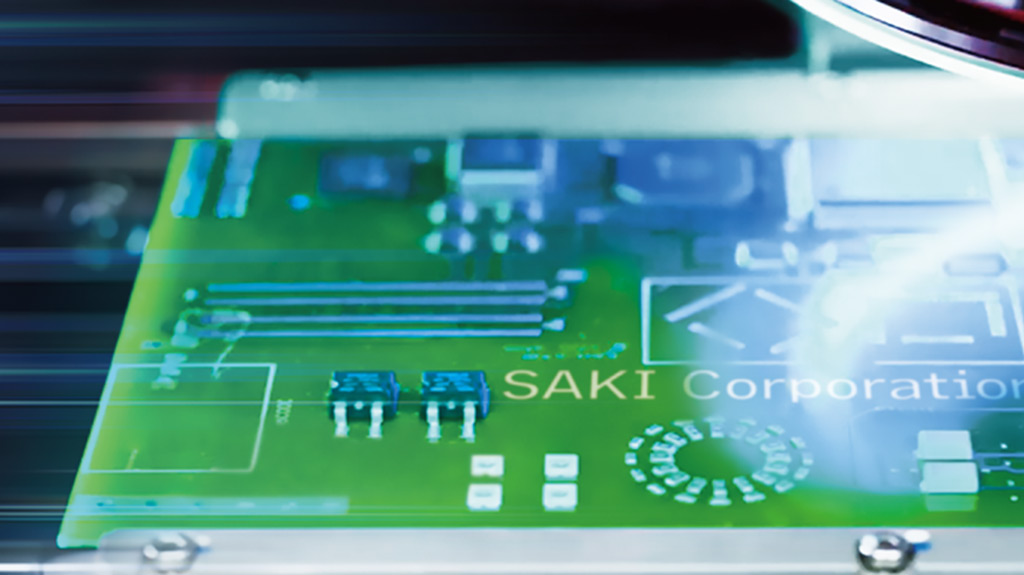
3D Image Acquisition Technology
Many of Saki’s original image processing technologies are used to obtain clear 3D images of the entire board surface.
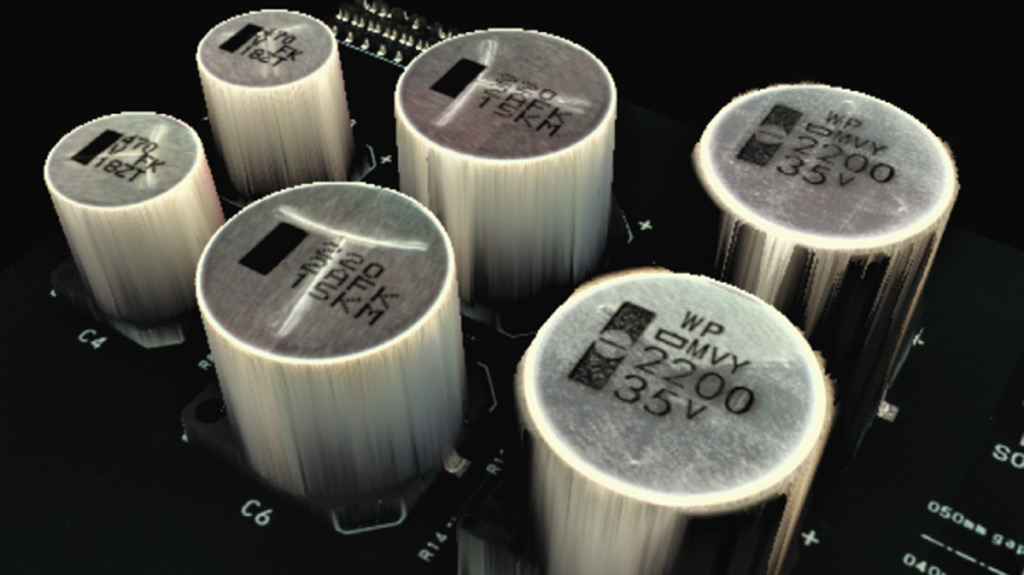
inview trigger
Product
3D-SPI
3D Solder Paste Inspection Machine
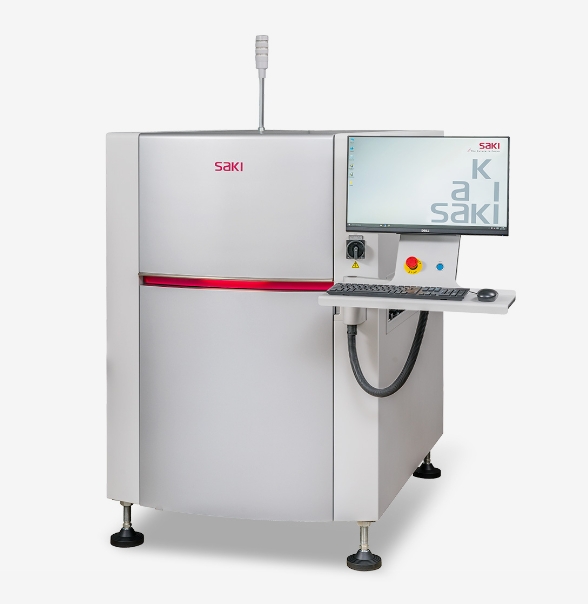
3D-AOI
3D Automated Optical Inspection Systems
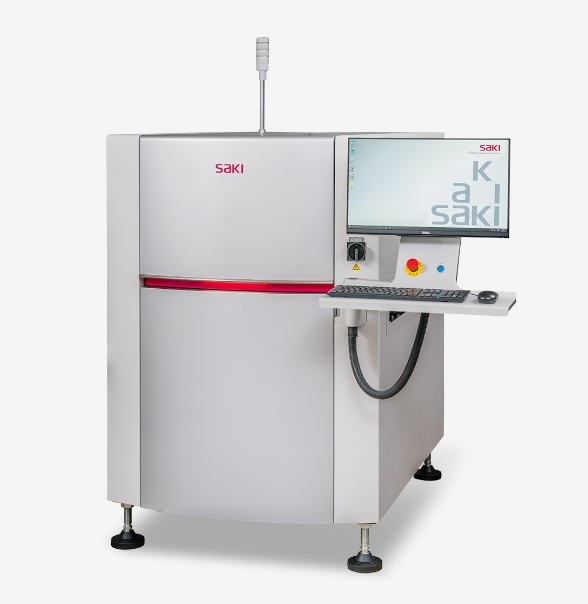
3D-CT AXI
Inline 3D-CT Automated X-ray Inspection Systems
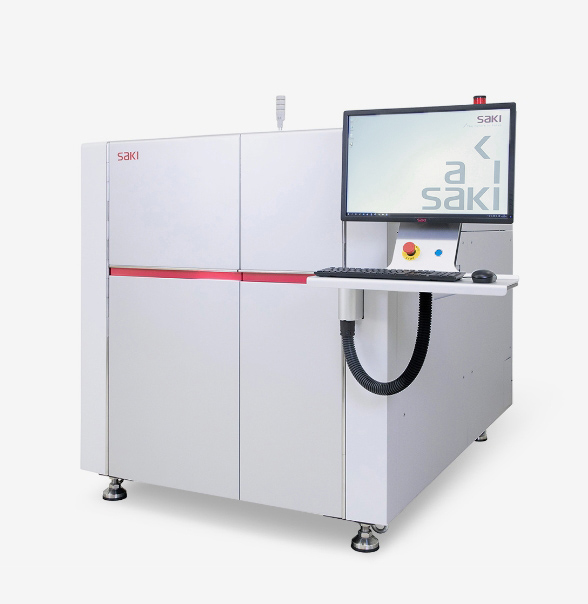
2D-AOI
2D Automated Optical Inspection Systems
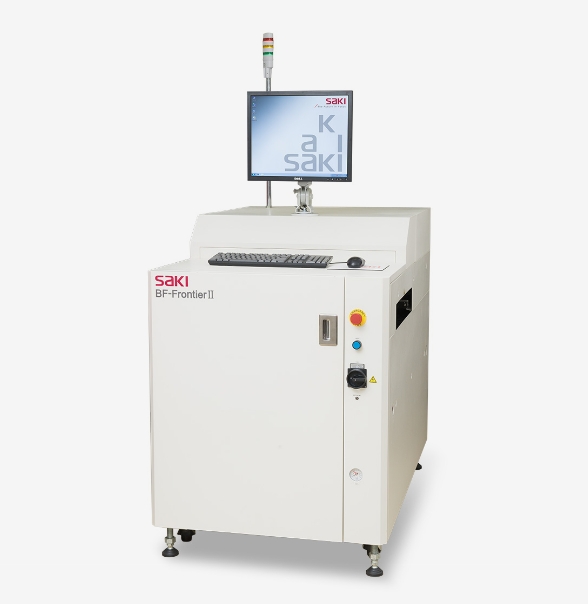
BottomSide-AOI
Inline Bottom-side 2D Automated
Optical Inspection Systems
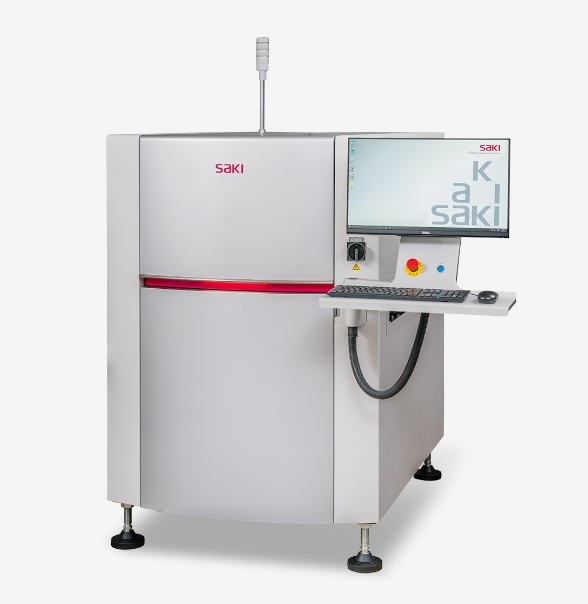
Power Module AXI
Inline 3D X-ray Inspection Machine for IGBT Power Modules
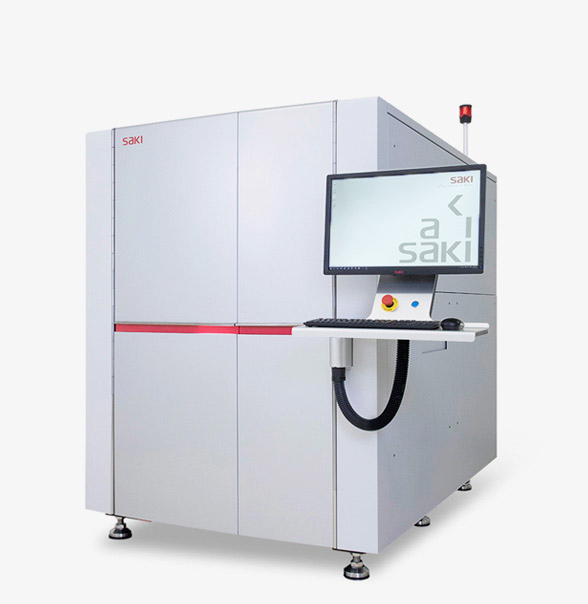
inview trigger
News release / Announcement
-
2025/07/02News releaseDriving Smart Manufacturing: Saki’s Inspection Systems Adopted by Alps Alpine
-
2025/07/01Announcement2D-AOI Products Discontinuation Announcement
-
2025/04/14News releaseSaki Corporation Relocates Nara Factory and Enhances Production Capacity
-
2025/04/08News releaseSaki’s AXI Upgrade Enhances Image Noise Reduction for Power Modules, Enabling Sharper, More Accurate Inspections
Event
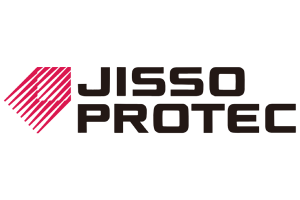
JISSO PROTEC 2025
Date
2025/06/04 – 06/06
Venue
Tokyo Big Sight
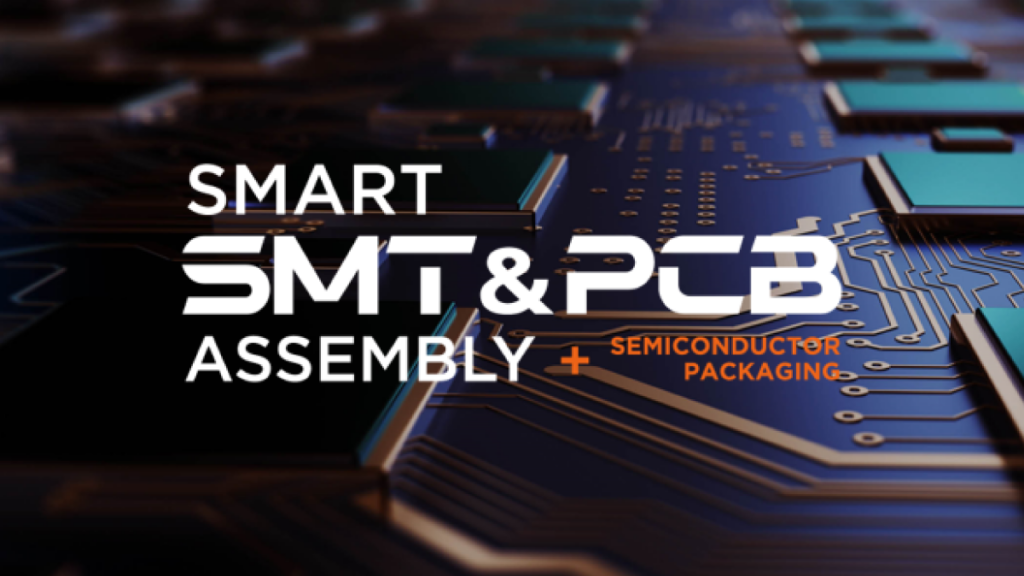
Smart SMT & PCB Assembly 2025
Date
2025/04/02 – 04/04
Venue
Suwon Convention Center
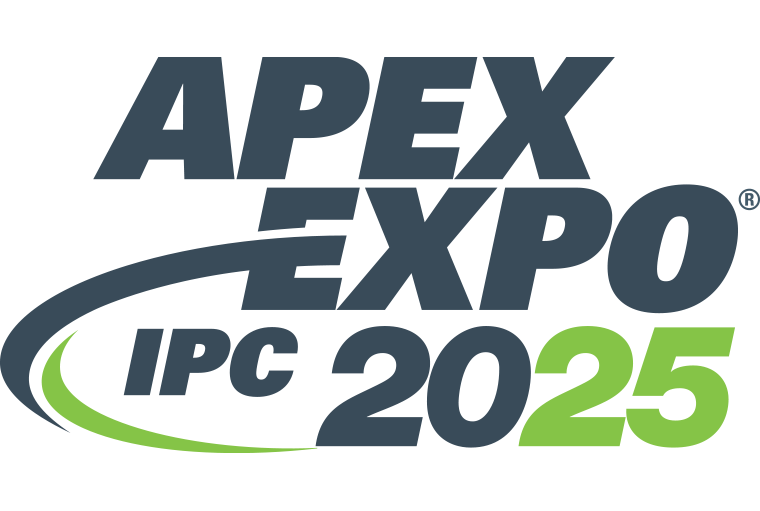
IPC APEX EXPO 2025
Date
2025/03/18 – 03/20
Venue
Anaheim Convention Center
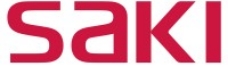
39th NEPCON JAPAN
Date
2025/01/22 – 01/24
Venue
Tokyo Big Sight

productronica India 2024
Date
2024/09/11 – 09/13
Venue
India Expo Centre, Greater Noida
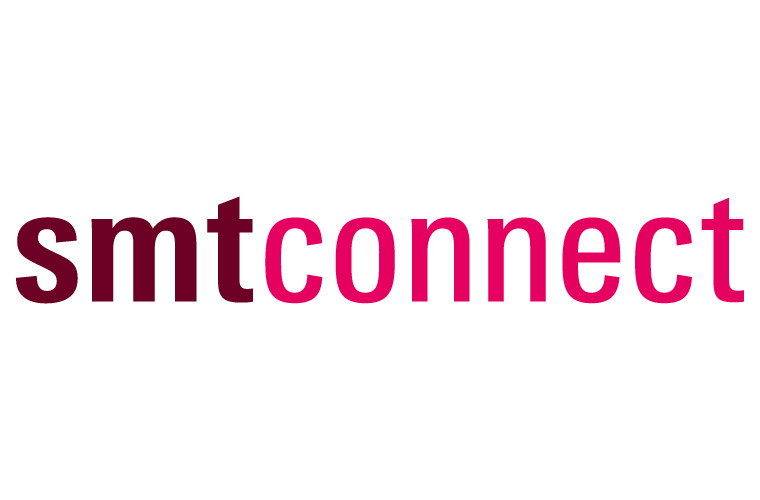
SMTConnect 2024
Date
2024/06/11 – 06/13
Venue
Exhibition Centre Nuremberg
About Us
Saki is a leading manufacturer of automated electronic assembly inspection equipment. Saki provides quality inspection solutions that determine a product’s viability by capturing and analyzing detailed imagery of the printed circuit board and components, replacing manual visual inspection with a highly accurate automated process. With a focus on power semiconductors and electronic substrates, Saki’s equipment delivers premium quality assurance for the electronic modules that are essential to the manufacture of electrical products.
Global Network
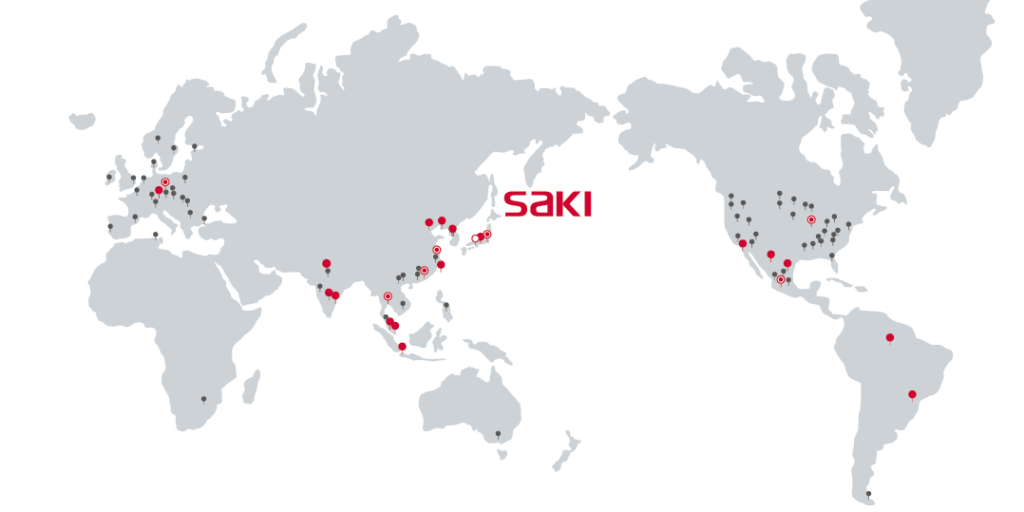