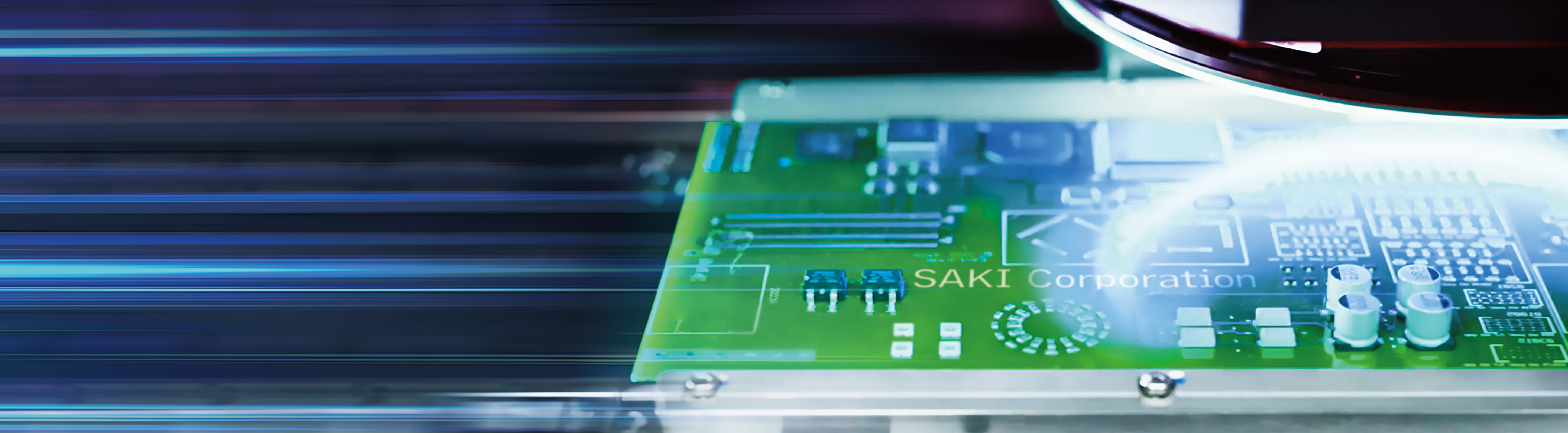
TECHNOLOGY
テクノロジー
サキは1994年の創業時、大手企業がひしめく検査機市場に独自の高速検査技術を携えて参入しました。以来、市場のニーズを日々感じ取りながら、新しい技術の開発に取り組んでいます。
サキの高度な検査を支える最新技術を紹介します。
SAKIテクノロジー
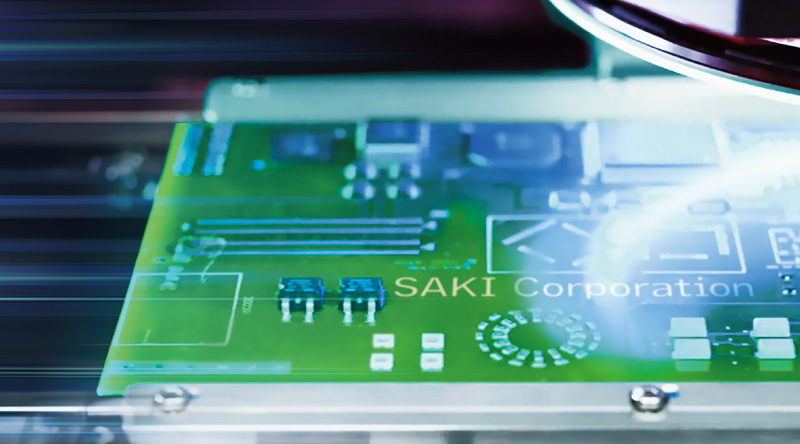
高速検査技術
サイクルタイムを短縮する広域撮像
光学ヘッドの高速移動を可能にするハードウェア構造
無駄なウェイティングタイムを減らす画像処理
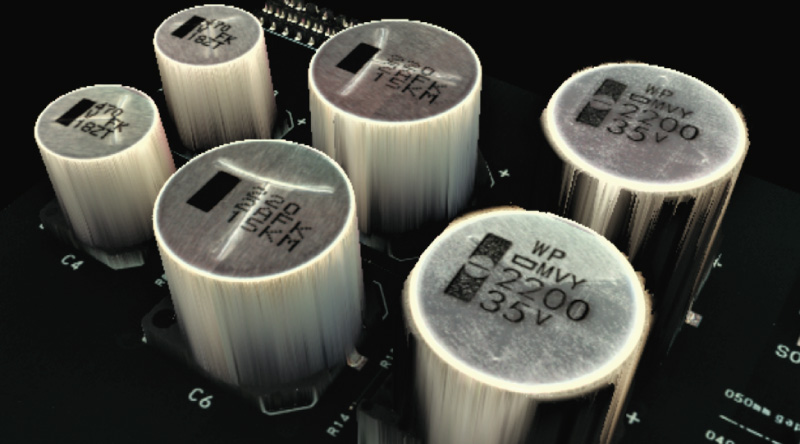
3次元画像取得技術
基板面補正技術
画像生成技術
ライブラリ管理工数の削減
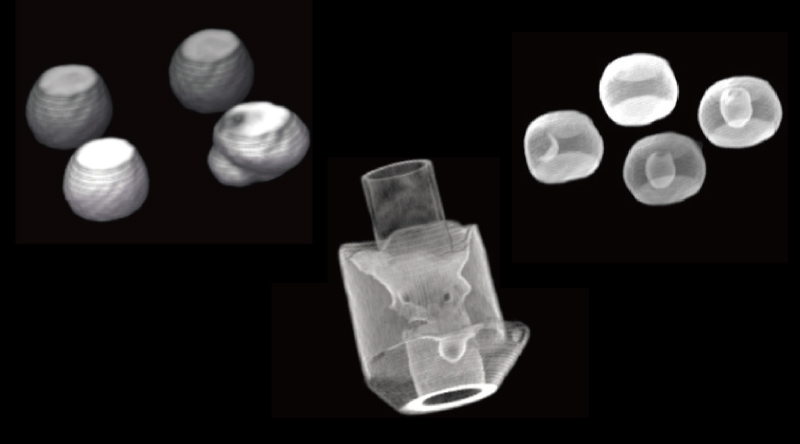
X線検査技術
サキの独自技術「プラナーCT方式」
不良検出力を上げる画像処理技術
インライン化にも対応する高速検査
SAKIソリューション
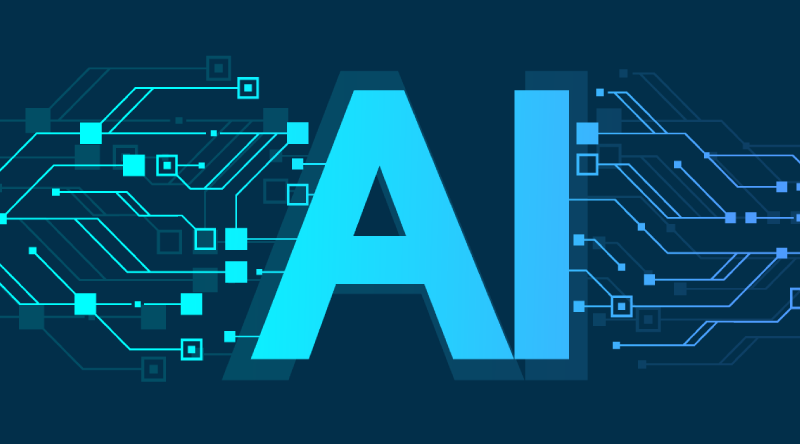
AI検査ソリューション
オペレーターの作業負担を軽減するAI再判定
AI検査(AI OCR)
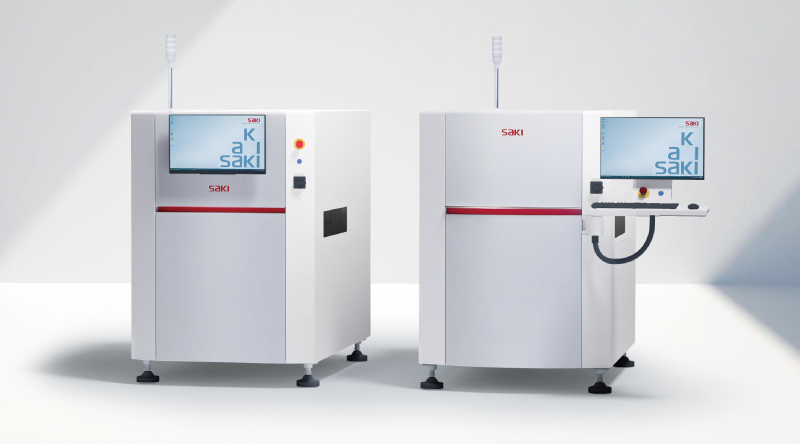
サキの設計思想 – Upgrade to Excellence –
検査ニーズに合わせてカスタマイズできるモジュール構造
検査ニーズに合わせて選択可能な拡張アイテム
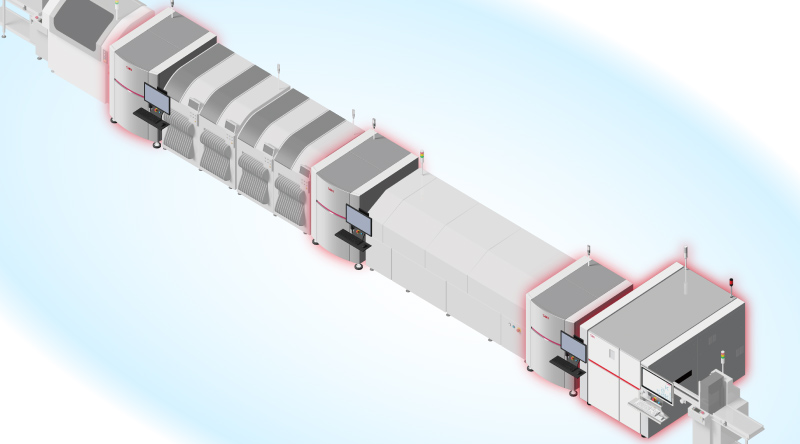
トータルソリューション
製品導入後のコスト削減と省人化
品質向上とスマートファクトリーの実現